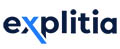
Wizualizacja danych – mniej oznacza więcej
Praktyka pokazuje, że systemy informatyczne wdrażane w zakładach produkcyjnych często nie są w pełni wykorzystywane przez pracowników. Wynika to zazwyczaj z nadmiaru informacji, które wymagają dogłębnej analizy.
Zbyt intensywne gromadzenie informacji w systemach prowadzi do wydłużenia czasu nauki nowego rozwiązania. Narzędzia stają się trudne w obsłudze – podczas gdy powinny być elastyczne. Dodatkowo uruchomienie, konfiguracja wykresów i ich analiza zajmują w takich przypadkach dużo czasu. A to sprawia, że pracownicy nie wykorzystują pełni możliwości nowoczesnych narzędzi.
Warto pamiętać, że lista zadań technologa czy operatora może być obszerna i wymagać dużego zaangażowania. Dlatego projektując systemy informatyczne, w pierwszym kroku warto zrealizować audyt. Umożliwia to zidentyfikowanie kluczowych parametrów, wskaźników i modułów, które będą efektywnie używane przez pracowników. Dzięki temu stworzony system będzie charakteryzować się przejrzystością i intuicyjnością, co przełoży się na łatwość przyswajania wiedzy. Z kolei użytkownikowi wystarczą zaledwie dwie minuty, aby przeanalizować informacje istotne dla jego działalności.
Między technologią a biznesem
W systemie informatycznym służącym do zbierania i analizy danych z różnego rodzaju maszyn i urządzeń wykorzystywany jest mechanizm wnioskowania. Dzieje się to poprzez:
Co istotne, informacje tego typu są często przekładane z terminologii technicznej na język bardziej przystępny dla środowiska biznesowego. Przykładowo zużycie energii może być bezpośrednio przeliczone na koszty w złotówkach. Dzięki temu system pełni rolę pośrednika między sektorem produkcji a obszarem biznesowym. Ulepsza to nie tylko standard przekazywanych danych, ale i ich dystrybucję. Ponadto ułatwia to zrozumienie i interpretację danych przez osoby odpowiedzialne za podejmowanie decyzji.
Przykład
W wielu zakładach przemysłowych powszechnym, a zarazem kosztownym surowcem jest sprężone powietrze. Z tego względu, jego pomiary i wizualizacje na interfejsie głównego panelu wizualizacyjnego są istotniejsze, niż prezentacja wielu skomplikowanych parametrów technicznych. Takie podejście warto stosować przy obliczaniu emisji CO2, ponieważ może mieć znaczny wpływ w kontekście polityki ESG.
Integracja informacji z różnych obszarów produkcyjnych
Analiza danych z wielu obszarów produkcji wymaga zrozumienia i integracji informacji pochodzących z różnorodnych warstw technologicznych, np. automatyki i elektrycznej. Dane generowane są przez szeroką gamę różnych czujników. Informacje te są pozyskiwane ze zdywersyfikowanych źródeł, w tym interfejsów API oraz baz danych SQL.
Wdrażając rozwiązanie IT należy umożliwić skuteczną analizę. Można to zrobić poprzez unifikację danych do spójnego formatu, dostosowanego do indywidualnych potrzeb klienta. Proces ten często wymaga
Projektując nowoczesne systemy SCADA (ang. Supervisory Control And Data Acquisition), warto mieć na uwadze aktualne tendencje. Przykładowo Situational Awareness znacząco różni od przestarzałych podejść. Kiedyś projektanci tworzyli interfejsy przeładowane różnorodnymi informacjami i grafikami, często skrywając dane w licznych oknach i komplikując nawigację. Utrudniało to efektywną analizę. Współczesne systemy SCADA charakteryzują się użyciem łagodnych odcieni szarości oraz prostotą wizualną. Przekłada się to na lepszą czytelność. Alarmy są natomiast prezentowane w jaskrawych kolorach, co zapobiega ich przeoczeniu i umożliwia szybkie podjęcie odpowiednich działań. Systemy SCADA oraz MES (ang. Manufacturing Execution System) wspomagają nie tylko monitoring zużycia energii elektrycznej, zarówno biernej jak i czynnej, ale również umożliwiają otrzymywanie alertów w sytuacjach wymagających uwagi. Przykładowo, włączona klimatyzacja i jednocześnie otwarte drzwi. Systemy te znajdują zastosowanie nie tylko w przemyśle, ale także w obszarze hotelarstwa czy administracji publicznej.
Jakie elementy powinny być wyświetlane jako priorytetowe? Tę kwestię powinien rozstrzygnąć audyt przedwykonawczy. Takie podejście pozwala na eliminację zbędnych danych i skupienie się na tych, które mają kluczowe znaczenie dla bezpieczeństwa i efektywności operacyjnej.
Przykład
Zakład produkcyjny zajmujący obszar niemal jednego hektara. Na tej rozległej powierzchni, rozlokowane zostały szafy elektryczne wyposażone w mierniki energii elektrycznej. Każdy z nich rejestrował około czterystu różnorodnych parametrów. Biorąc pod uwagę, że na całym terenie znajdowało się kilkadziesiąt takich urządzeń, łatwo zrozumieć, że gromadzone przez nie dane nie były efektywnie analizowane. Z uwagi na ich ogromną liczbę i rozproszenie, taki proces wydawał się być niezwykle trudny.
W odpowiedzi na te wyzwania firma explitia opracowała zaawansowany system informatyczny, który pozwolił na centralizację wszystkich zebranych danych na serwerze OPC. Rozwiązanie to nie tylko umożliwiło efektowną wizualizację danych, ale przede wszystkim zaoferowało możliwość szczegółowej analizy wybranych parametrów. Dzięki temu zakład zyskał narzędzie pozwalające na głębsze zrozumienie wykorzystania energii, oparte na precyzyjnym badaniu rzeczywistego stanu zużycia.
Niezależne metody kontroli procesów
W wielu zakładach produkcyjnych technolodzy często stają przed wyzwaniem samodzielnego porównywania i weryfikacji danych zebranych w postaci trendów. Dzięki temu mogą sprawdzić, czy nie odbiegają one od ustalonych norm. Ten proces wymaga jednak nie tylko odpowiedniej wiedzy i umiejętności, ale jest również czasochłonny i podatny na błędy.
Z pomocą przychodzi System Statystycznej Kontroli Procesu (SPC). Rozwiązanie samo się uczy i automatyzuje analizę procesów. Dzięki temu eliminuje konieczność specjalistycznej wiedzy ze strony osoby zatrudnionej. Obsługa systemu SPC jest intuicyjna, a pracownik jest informowany o potencjalnych problemach poprzez proste komunikaty mailowe, np. ostrzeżenia o zbliżaniu się do granicznych poziomów.
Andon OEE Wskaźnik OEE znacznie ułatwia ocenę dostępności, jakości i wydajności procesów produkcyjnych. Prezentuje bowiem kluczowe informacje w sposób prosty i przystępny, wykorzystując procentowe dane i przejrzystą kolorystykę. Wizualizacja tego wskaźnika może być dostępna m.in. na:
Analiza danych jakościowych za pomocą MES
Systemy klasy MES, automatyzując proces kontroli jakości każdej sztuki na poszczególnych etapach produkcji, pozwalają m.in. na szybką, dwuminutową analizę jakościową. W przeciwieństwie do tradycyjnych metod (manualnej kontroli) – system automatycznie weryfikuje zgodność produktu z wymaganymi parametrami. Obejmuje to także poprawność realizacji zlecenia przez operatora oraz odpowiednią konfigurację maszyny dla danego typu produktu. System MES, taki jak Portal Produkcyjny, dostarcza również raporty podkreślające wszelkie odstępstwa od ustalonych standardów. Znacznie ułatwia to identyfikację problemów, bez potrzeby ciągłego monitorowania trendów lub parametrów maszynowych.
Zarządzanie zleceniami produkcyjnymi
Zasada dwóch minut stanowi fundament w efektywnym zarządzaniu zleceniami produkcyjnymi. Implementacja intuicyjnego interfejsu umożliwia operatorom błyskawiczne i bezproblemowe zarządzanie procesami zleceniowymi. System powinien jednocześnie być zintegrowany z innymi modułami i zaprojektowany z myślą o maksymalnym uproszczeniu operacji. Działanie operatora sprowadza się wtedy do uruchomienia i zakończenia zlecenia, a wszystkie inne czynności odbywają się w sposób automatyczny. Wdrożenie opisanej szczegółowo zasady dwóch minut jest kluczowe w zarządzaniu procesami produkcyjnymi, a także w analizie danych. Sprawny dostęp do rzetelnych informacji pomaga podejmować trafne decyzje biznesowe. A w efekcie – zwiększać produktywność i redukować koszty operacyjne. Ta prosta, lecz rewolucyjna zasada, może znacząco przyczynić się do wzrostu wydajności w każdym zakładzie produkcyjnym.
Autor: Dawid Krawczyk, Project manager explitia
Źródło: www.explitia.com
Praktyka pokazuje, że systemy informatyczne wdrażane w zakładach produkcyjnych często nie są w pełni wykorzystywane przez pracowników. Wynika to zazwyczaj z nadmiaru informacji, które wymagają dogłębnej analizy.
Zbyt intensywne gromadzenie informacji w systemach prowadzi do wydłużenia czasu nauki nowego rozwiązania. Narzędzia stają się trudne w obsłudze – podczas gdy powinny być elastyczne. Dodatkowo uruchomienie, konfiguracja wykresów i ich analiza zajmują w takich przypadkach dużo czasu. A to sprawia, że pracownicy nie wykorzystują pełni możliwości nowoczesnych narzędzi.
Warto pamiętać, że lista zadań technologa czy operatora może być obszerna i wymagać dużego zaangażowania. Dlatego projektując systemy informatyczne, w pierwszym kroku warto zrealizować audyt. Umożliwia to zidentyfikowanie kluczowych parametrów, wskaźników i modułów, które będą efektywnie używane przez pracowników. Dzięki temu stworzony system będzie charakteryzować się przejrzystością i intuicyjnością, co przełoży się na łatwość przyswajania wiedzy. Z kolei użytkownikowi wystarczą zaledwie dwie minuty, aby przeanalizować informacje istotne dla jego działalności.
Między technologią a biznesem
W systemie informatycznym służącym do zbierania i analizy danych z różnego rodzaju maszyn i urządzeń wykorzystywany jest mechanizm wnioskowania. Dzieje się to poprzez:
- uproszczenie informacji;
- spłaszczenie szczegółów do prostego wskaźnika „tak”, „nie” lub procentowego.
Co istotne, informacje tego typu są często przekładane z terminologii technicznej na język bardziej przystępny dla środowiska biznesowego. Przykładowo zużycie energii może być bezpośrednio przeliczone na koszty w złotówkach. Dzięki temu system pełni rolę pośrednika między sektorem produkcji a obszarem biznesowym. Ulepsza to nie tylko standard przekazywanych danych, ale i ich dystrybucję. Ponadto ułatwia to zrozumienie i interpretację danych przez osoby odpowiedzialne za podejmowanie decyzji.
Przykład
W wielu zakładach przemysłowych powszechnym, a zarazem kosztownym surowcem jest sprężone powietrze. Z tego względu, jego pomiary i wizualizacje na interfejsie głównego panelu wizualizacyjnego są istotniejsze, niż prezentacja wielu skomplikowanych parametrów technicznych. Takie podejście warto stosować przy obliczaniu emisji CO2, ponieważ może mieć znaczny wpływ w kontekście polityki ESG.
Integracja informacji z różnych obszarów produkcyjnych
Analiza danych z wielu obszarów produkcji wymaga zrozumienia i integracji informacji pochodzących z różnorodnych warstw technologicznych, np. automatyki i elektrycznej. Dane generowane są przez szeroką gamę różnych czujników. Informacje te są pozyskiwane ze zdywersyfikowanych źródeł, w tym interfejsów API oraz baz danych SQL.
Wdrażając rozwiązanie IT należy umożliwić skuteczną analizę. Można to zrobić poprzez unifikację danych do spójnego formatu, dostosowanego do indywidualnych potrzeb klienta. Proces ten często wymaga
- agregacji danych na serwerach OPC;
- dystrybucji danych za pomocą odpowiednich protokołów do systemów zarządzania na wyższym poziomie;
- integracji wszystkich zebranych informacji w jednej, relacyjnej bazie danych SQL.
Projektując nowoczesne systemy SCADA (ang. Supervisory Control And Data Acquisition), warto mieć na uwadze aktualne tendencje. Przykładowo Situational Awareness znacząco różni od przestarzałych podejść. Kiedyś projektanci tworzyli interfejsy przeładowane różnorodnymi informacjami i grafikami, często skrywając dane w licznych oknach i komplikując nawigację. Utrudniało to efektywną analizę. Współczesne systemy SCADA charakteryzują się użyciem łagodnych odcieni szarości oraz prostotą wizualną. Przekłada się to na lepszą czytelność. Alarmy są natomiast prezentowane w jaskrawych kolorach, co zapobiega ich przeoczeniu i umożliwia szybkie podjęcie odpowiednich działań. Systemy SCADA oraz MES (ang. Manufacturing Execution System) wspomagają nie tylko monitoring zużycia energii elektrycznej, zarówno biernej jak i czynnej, ale również umożliwiają otrzymywanie alertów w sytuacjach wymagających uwagi. Przykładowo, włączona klimatyzacja i jednocześnie otwarte drzwi. Systemy te znajdują zastosowanie nie tylko w przemyśle, ale także w obszarze hotelarstwa czy administracji publicznej.
Jakie elementy powinny być wyświetlane jako priorytetowe? Tę kwestię powinien rozstrzygnąć audyt przedwykonawczy. Takie podejście pozwala na eliminację zbędnych danych i skupienie się na tych, które mają kluczowe znaczenie dla bezpieczeństwa i efektywności operacyjnej.
Przykład
Zakład produkcyjny zajmujący obszar niemal jednego hektara. Na tej rozległej powierzchni, rozlokowane zostały szafy elektryczne wyposażone w mierniki energii elektrycznej. Każdy z nich rejestrował około czterystu różnorodnych parametrów. Biorąc pod uwagę, że na całym terenie znajdowało się kilkadziesiąt takich urządzeń, łatwo zrozumieć, że gromadzone przez nie dane nie były efektywnie analizowane. Z uwagi na ich ogromną liczbę i rozproszenie, taki proces wydawał się być niezwykle trudny.
W odpowiedzi na te wyzwania firma explitia opracowała zaawansowany system informatyczny, który pozwolił na centralizację wszystkich zebranych danych na serwerze OPC. Rozwiązanie to nie tylko umożliwiło efektowną wizualizację danych, ale przede wszystkim zaoferowało możliwość szczegółowej analizy wybranych parametrów. Dzięki temu zakład zyskał narzędzie pozwalające na głębsze zrozumienie wykorzystania energii, oparte na precyzyjnym badaniu rzeczywistego stanu zużycia.
Niezależne metody kontroli procesów
W wielu zakładach produkcyjnych technolodzy często stają przed wyzwaniem samodzielnego porównywania i weryfikacji danych zebranych w postaci trendów. Dzięki temu mogą sprawdzić, czy nie odbiegają one od ustalonych norm. Ten proces wymaga jednak nie tylko odpowiedniej wiedzy i umiejętności, ale jest również czasochłonny i podatny na błędy.
Z pomocą przychodzi System Statystycznej Kontroli Procesu (SPC). Rozwiązanie samo się uczy i automatyzuje analizę procesów. Dzięki temu eliminuje konieczność specjalistycznej wiedzy ze strony osoby zatrudnionej. Obsługa systemu SPC jest intuicyjna, a pracownik jest informowany o potencjalnych problemach poprzez proste komunikaty mailowe, np. ostrzeżenia o zbliżaniu się do granicznych poziomów.
Andon OEE Wskaźnik OEE znacznie ułatwia ocenę dostępności, jakości i wydajności procesów produkcyjnych. Prezentuje bowiem kluczowe informacje w sposób prosty i przystępny, wykorzystując procentowe dane i przejrzystą kolorystykę. Wizualizacja tego wskaźnika może być dostępna m.in. na:
- komputerach w biurach zarządzających;
- wielkogabarytowych ekranach w halach produkcyjnych;
- interfejsach HMI dostępnych dla operatorów.
Analiza danych jakościowych za pomocą MES
Systemy klasy MES, automatyzując proces kontroli jakości każdej sztuki na poszczególnych etapach produkcji, pozwalają m.in. na szybką, dwuminutową analizę jakościową. W przeciwieństwie do tradycyjnych metod (manualnej kontroli) – system automatycznie weryfikuje zgodność produktu z wymaganymi parametrami. Obejmuje to także poprawność realizacji zlecenia przez operatora oraz odpowiednią konfigurację maszyny dla danego typu produktu. System MES, taki jak Portal Produkcyjny, dostarcza również raporty podkreślające wszelkie odstępstwa od ustalonych standardów. Znacznie ułatwia to identyfikację problemów, bez potrzeby ciągłego monitorowania trendów lub parametrów maszynowych.
Zarządzanie zleceniami produkcyjnymi
Zasada dwóch minut stanowi fundament w efektywnym zarządzaniu zleceniami produkcyjnymi. Implementacja intuicyjnego interfejsu umożliwia operatorom błyskawiczne i bezproblemowe zarządzanie procesami zleceniowymi. System powinien jednocześnie być zintegrowany z innymi modułami i zaprojektowany z myślą o maksymalnym uproszczeniu operacji. Działanie operatora sprowadza się wtedy do uruchomienia i zakończenia zlecenia, a wszystkie inne czynności odbywają się w sposób automatyczny. Wdrożenie opisanej szczegółowo zasady dwóch minut jest kluczowe w zarządzaniu procesami produkcyjnymi, a także w analizie danych. Sprawny dostęp do rzetelnych informacji pomaga podejmować trafne decyzje biznesowe. A w efekcie – zwiększać produktywność i redukować koszty operacyjne. Ta prosta, lecz rewolucyjna zasada, może znacząco przyczynić się do wzrostu wydajności w każdym zakładzie produkcyjnym.
Autor: Dawid Krawczyk, Project manager explitia
Źródło: www.explitia.com